▪︎ Happy Society Policy and Goals

KISCO prioritizes the safety and human rights of all stakeholders including employees, partners in the supply chain, and members of the local community, based on the values of diversity and inclusion. We aim to foster mutual growth and smooth communication with our stakeholders, striving for a better life for all.
|
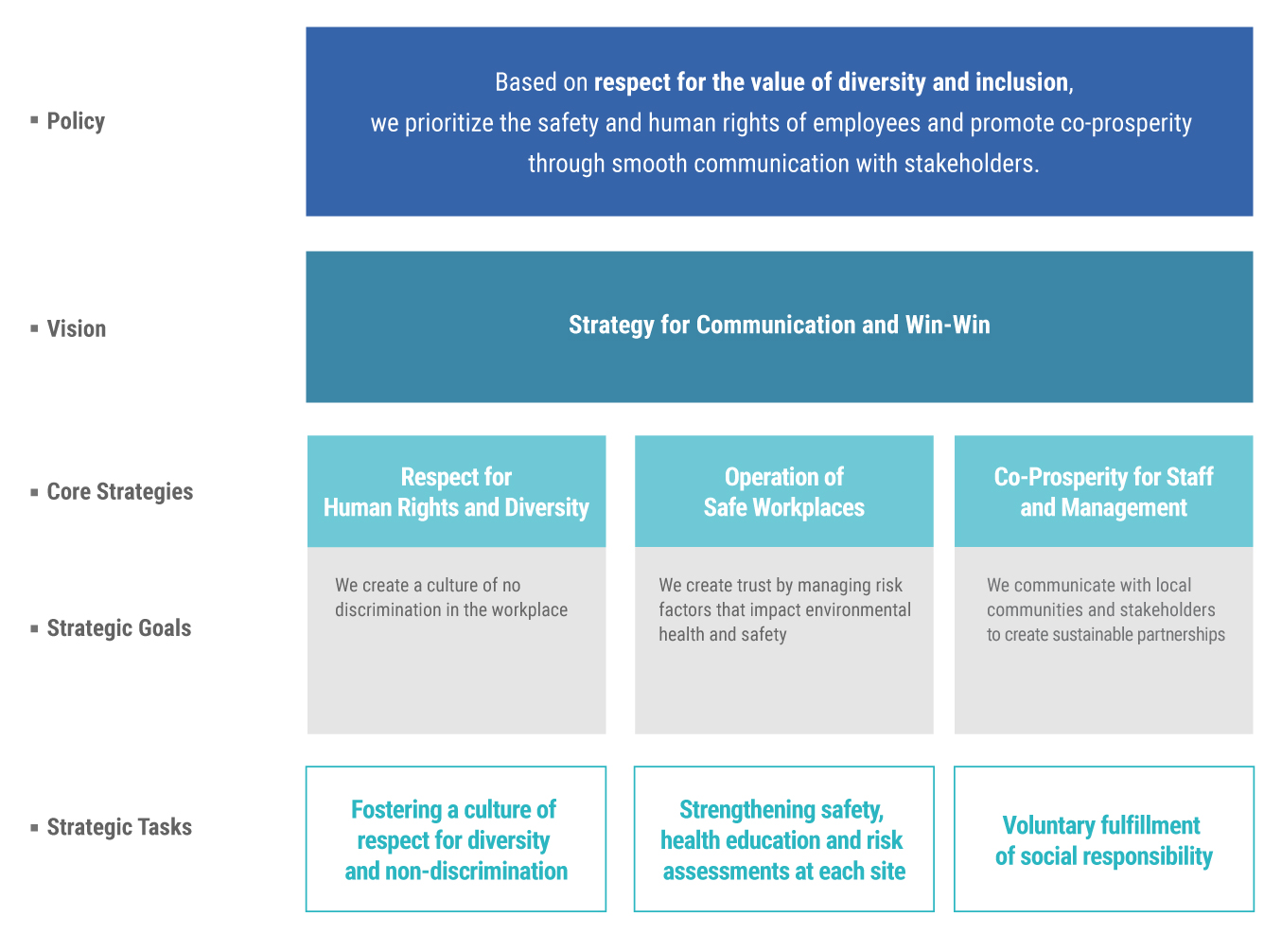
▪︎ Talent Management Policy and Goals

KISCO is committed to developing talented individuals who are the foundation of corporate competitiveness, under the belief that “people are our greatest asset.” Based on our corporate philosophy of “Harmony, Creativity and Effort,” we pursue human-centered management by establishing a fair personnel management system including recruitment, evaluation, and reasonable compensation based on performance and ability to motivate employees and enhance performance.
|
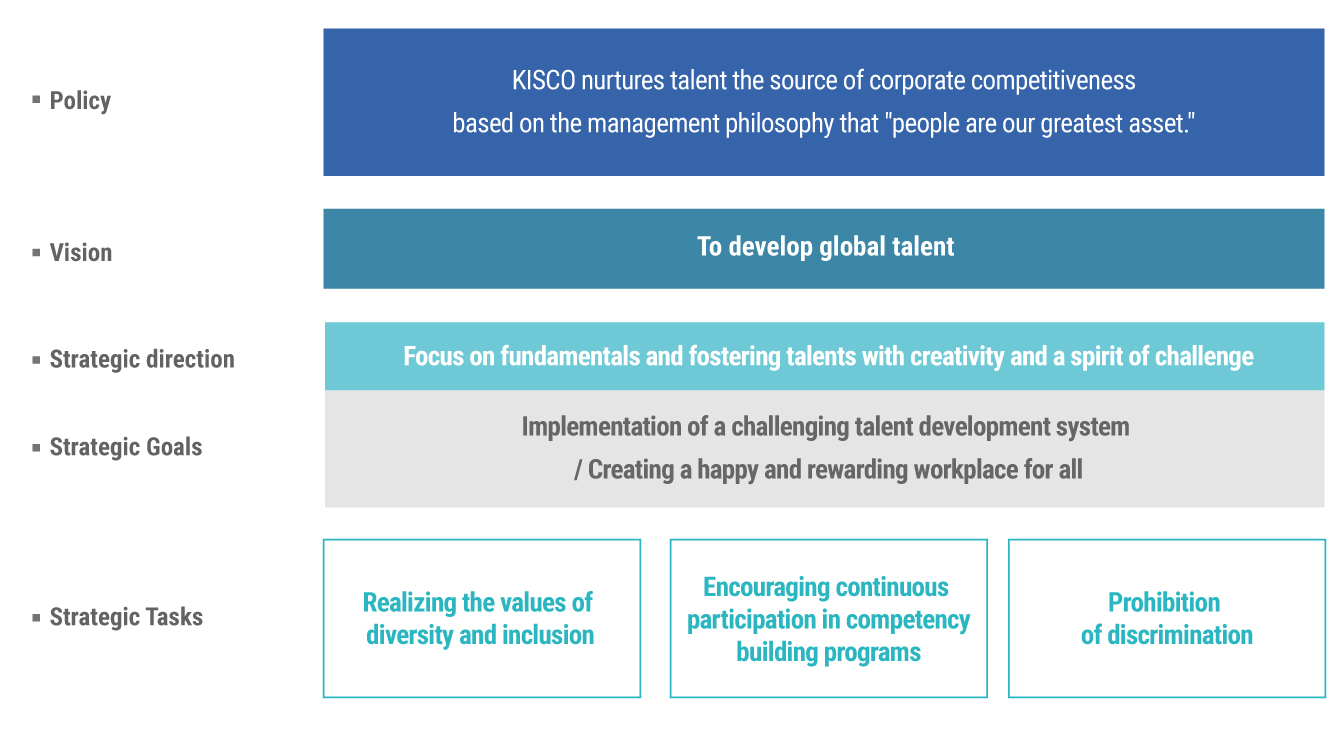
▪︎ Status of HR
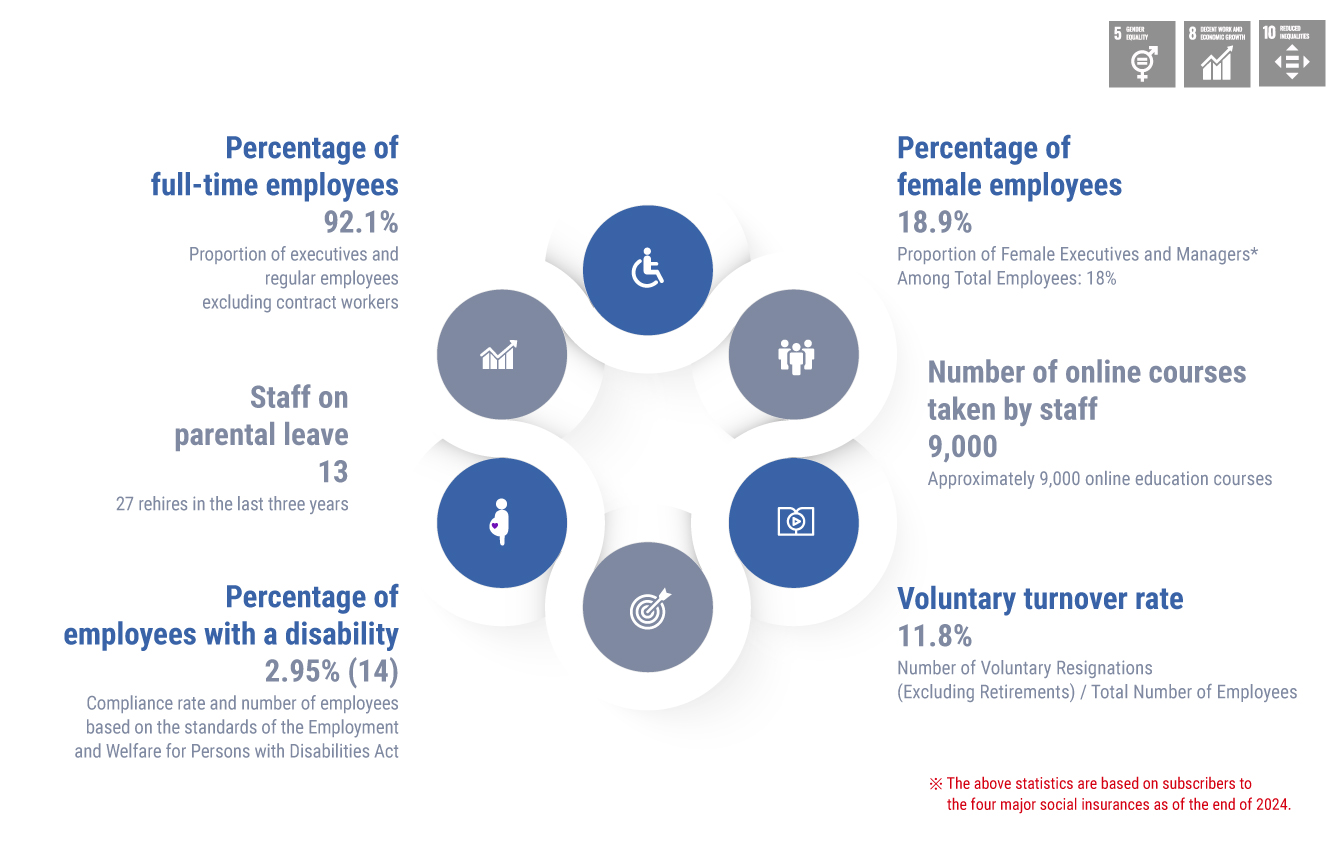
Employee Status |
2022 |
2023 |
2024 |
Remarks |
Employee numbers |
Total employee numbers |
586 |
534 |
491 |
|
Workers with no fixed contract |
538 |
487 |
452 |
Out of 16 fixed term workers, 9 employees were
re-employed (as of 2024) |
Fixed-term worker |
23 |
21 |
16 |
Diversity |
Mandatory employment of
people with disabilities |
3.3%
(20) |
3.1%
(16) |
3.0%
(14) |
To promote diversity and inclusivity,
we give preference points to applicants with
disabilities during employee recruitment.
We achieve this through inclusive hiring practices
and we ensure that social teams and workplace facilities
include provisions for people with disabilities. |
Percentage of female employees |
17.6%
(103) |
18.4%
(98) |
18.9%
(93) |
Proportion of Female Managers* (Excluding Executives): 19.4% |
Percentage of female executives |
12.0%
(3) |
12.0%
(3) |
13.0%
(3) |
Proportion of female executives among all executives
|
Foreign employees |
6 |
6 |
6 |
In order to recruit excellent foreign employees,
we are making continuous efforts such as attending
the international student recruitment fair. |
* |
Manager: Team leaders and section heads responsible for managing and supervising one or more departments or team members |
▪︎ Human Resource Development

KISCO clearly defines the roles and responsibilities required by each position and rank and operates a structured training program to develop competencies aligned with those roles. This helps foster talent that contributes to company-wide performance. Programs include onboarding training for new hires and promotees, leadership development by position, financial education, and more. We also provide a wide range of online courses on job skills, communication, performance management, languages, etc., allowing employees to learn easily and conveniently anytime, anywhere. Currently, around 9,000 courses are available through the internal intranet. Additionally, employee surveys and training satisfaction evaluations are used to gather feedback and continuously improve and refine the training programs.
|
▪︎
Employee Training |
Year |
2022 |
2023 |
2024 |
Average training hours per employee |
Time/ number |
26.9 |
24.9 |
24.6 |
|
– |
Average training hours = Total training hours / total employees |
– |
Employee training hours include the four mandatory legal trainings*, industrial safety and health education, and external training (including online learning platforms). |
* |
The four mandatory legal trainings are required by Korean law for all employees and include: sexual harassment prevention, awareness training on disabilities in the workplace, personal information protection, and retirement pension education. |
▪︎ Application for KISCO Cyber Training Institute |
|
KISCO operates the “KISCO Cyber Training Institute” in collaboration with professional educational institutions, enabling employees to freely select and take various programs for developing job skills.
|
▪︎ 2024 Cyber Training Institute Competency Development Program Enrollment Status |
▪︎
Education Classification |
Types of Detailed Courses |
Completion Programs¹﹚
(Units) |
Number of Completion²﹚
(Individuals) |
Completion hours²﹚
(Individuals) |
Common / Job-specific |
Management Insight, Business Functions, Shared Values, Business Skills, IT, MBA, QA, etc. |
38 |
35 |
315 |
Leadership |
General Leadership, People Management, Task Management, Self-Management, Organizational Management, etc. |
20 |
20 |
102 |
Foreign Languages |
English, Japanese, Chinese, Other Languages |
19 |
14 |
166 |
Industry-specific Professional Skills |
Manufacturing, Trade/Logistics/Distribution, Engineering Basics, Construction, Finance, General Medicine, etc. |
9 |
9 |
185 |
Liberal Arts Education |
Topics include humanities, general culture, family-friendly programs, cultural lectures, arts, financial planning, etc. |
3 |
4 |
22 |
Certification |
IT/OA, Manufacturing/Environment/Industry, Logistics/Distribution/Purchasing, Service, Taxation/Accounting, Safety, etc. |
2 |
1 |
36 |
Total |
91 |
83 |
826 |
|
1) |
Number of courses actually completed by KISCO employees out of approximately 9,000 available programs. |
2) |
Cumulative number of participants and total completion hours in 2024. |
▪︎ Status of Seminar Operations in 2024 |
|
KISCO actively encourages participation in seminars provided by domestic and foreign institutions, and customers. These seminars enable KISCO staff to acquire diverse knowledge and broaden their perspectives.
|
▪︎
Host |
Types of Detailed Processes |
Number of Courses Attended¹﹚ |
Number of Attendees²﹚ |
Duration of Attendance (Hours)³﹚ |
Domestic and International Institutions |
Current Issues, ESG, Economic Outlook, AI, Personnel Management, etc. |
21 |
27 |
54 |
Clients |
Financial Markets, ESG, Digital Trends, Major Accidents Penalty Act, Leadership, etc. |
9 |
84 |
168 |
Total |
30 |
111 |
222 |
|
1) |
Number of external seminar sessions completed by KISCO employees among those announced in 2024. |
2) |
Cumulative number of participants and total learning hours in 2024. |
▪︎ Respect for Human Rights
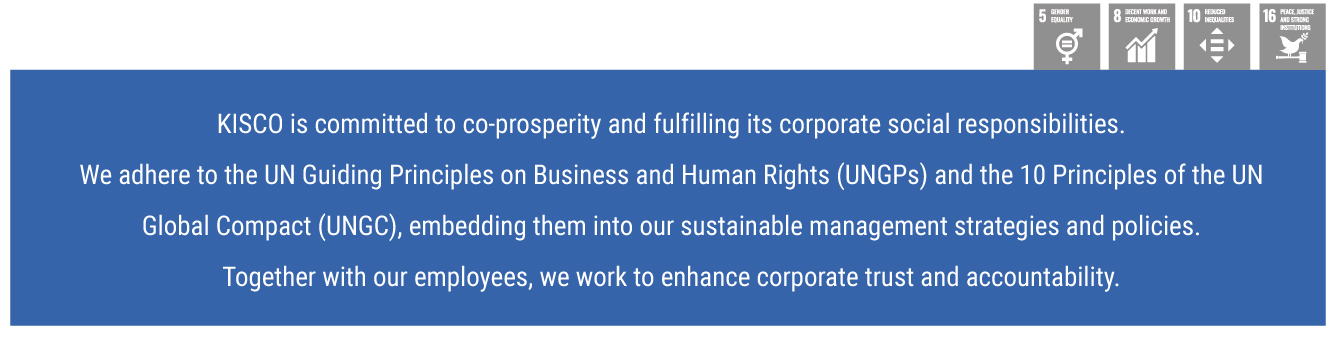
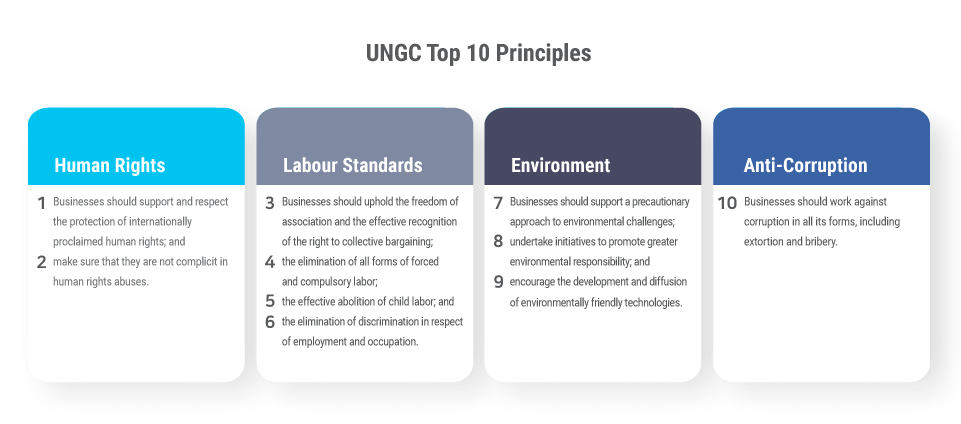
The KISCO Code of Ethics provides standards for decision-making, and behavior based on compliance with laws and ethical conduct, aiming to fulfill corporate social responsibility through proper business practices. It outlines policies such as non-discrimination/equal opportunity, mutual respect, and human rights protection for employees, partners, customers, and shareholders. The code prohibits forced labor, wage exploitation, and child labor, while also promoting respect for diversity, non-discrimination, and reasonable conflict resolution.
KISCO also complies with the Korean Labor Standards Act and the Maternal Protection Act and maintains internal policies in alignment with these laws.
▸ Download KISCO Code of Ethics
|
▪︎ Human Rights Violation Prevention Program

▪︎ Frequent Human Rights Violation Prevention Programs
|
▪︎
Category |
Frequency |
Training hour per person |
Target of training |
Sexual harassment prevention education |
Annual |
Over 1 hour |
All employees |
Anti-bullying education in the workplace |
Annual |
Over 1 hour |
All employees |
Education to improve awareness of people with disabilities |
Annual |
Over 1 hour |
All employees |
Personal information security education |
Annual |
Over 1 hour |
All employees |
Industrial health and safety education |
Branching |
Over 3 hours |
All employees |
Training for new hires |
Occasional |
8 hours |
New hires |
Human rights education in onboarding |
Occasional |
Over 1 hour |
New hires |
▪︎ Conduct an In-house Campaign
|
▪︎
▪︎ Complaint Handling
KISCO operates a grievance handling process that allows employees to report issues anonymously through designated grievance officers. The scope of grievances includes occupational health and safety concerns as well as issues related to human rights, labor, environment, and anti-corruption in line with the UNGC’s 10 Principles of Corporate Social Responsibility. The process also covers workplace harassment, sexual harassment, and other human rights violations. In addition, KISCO conducts regular consultations with on-site partner companies to gather feedback.
* Number of grievances received in 2024: 0 cases
|
▪︎ Complaint Handling Process
|

▪︎ Information Protection System
KISCO complies with the Global Cloud Compliance Program by maintaining strong control features, as well as cloud security and compliance. KISCO meets the requirements of relevant compliance or audit standards and provides an environment suitable for governance-focused audits. |
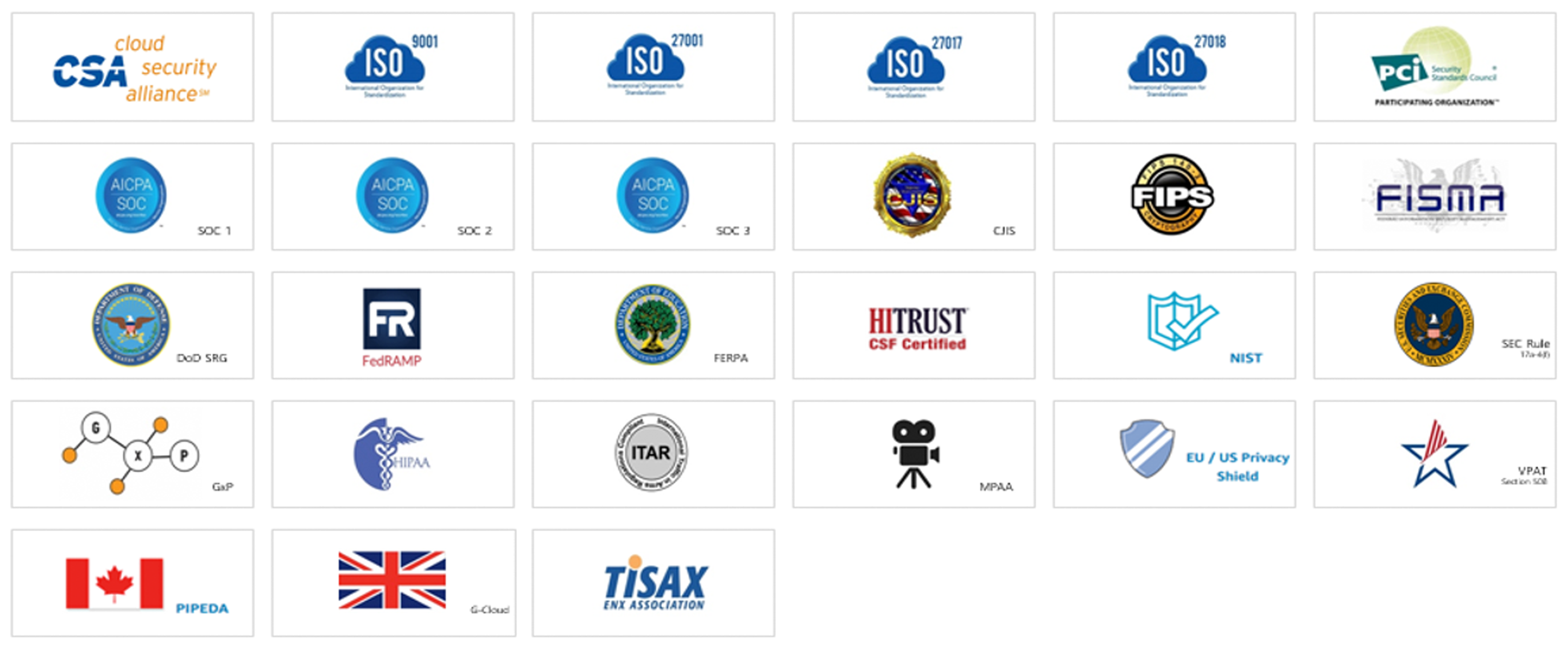
▪︎ Conduct Annual, Occasional Verification of System Stability
|
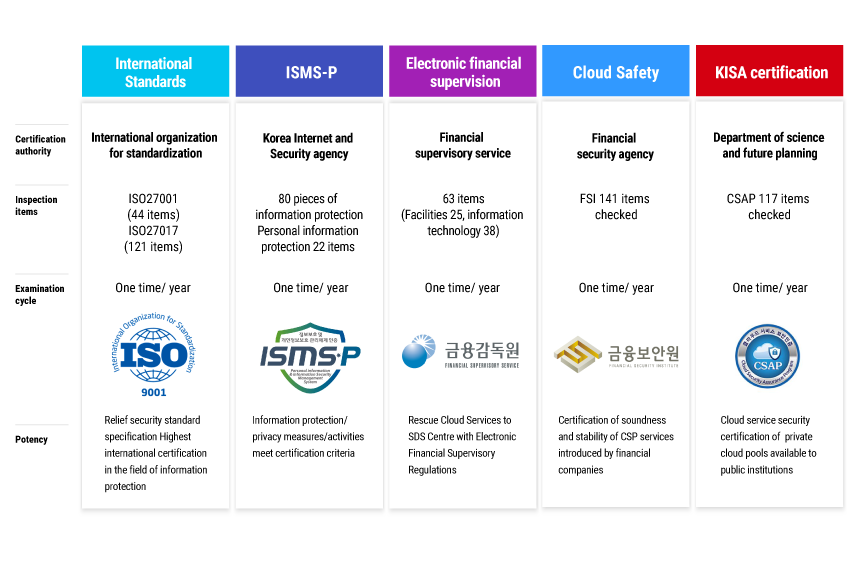
▪︎ Performing Vulnerability Analysis for Secure In-house Information Protection
|
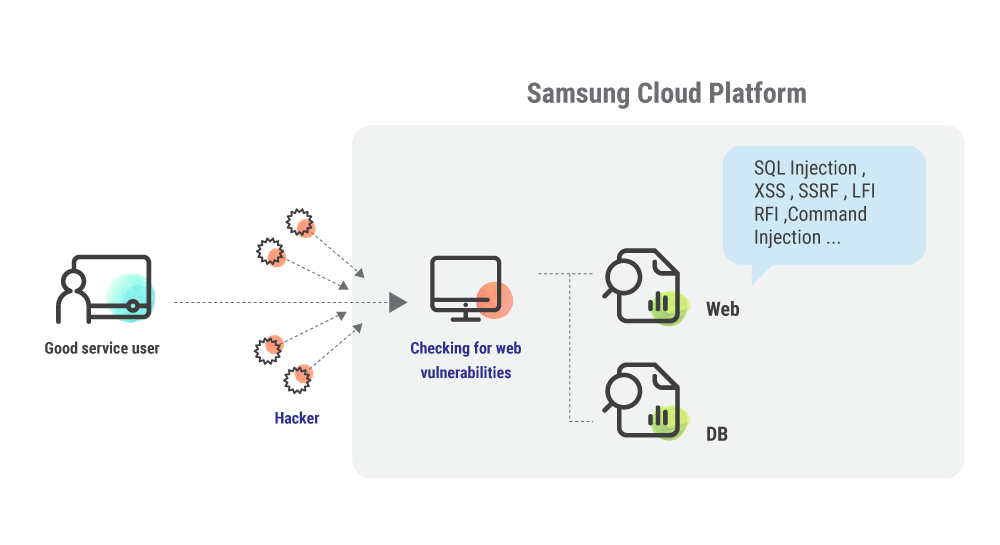
▪︎ Work-life Balance
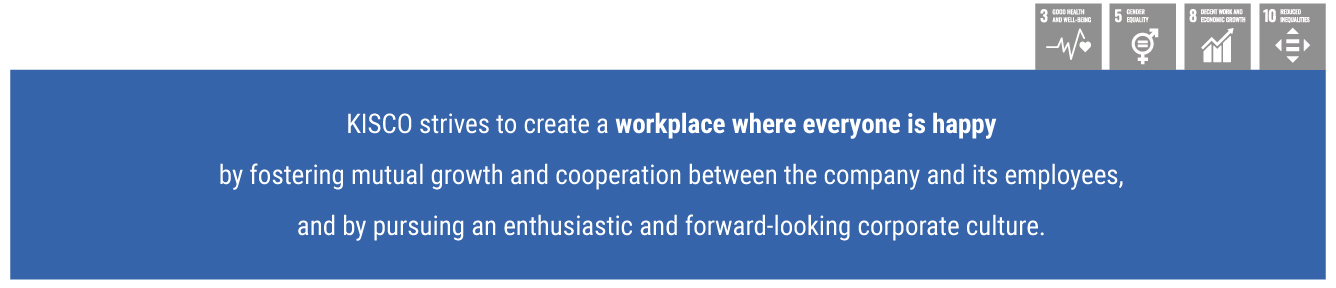
KISCO operates various related systems to create a healthy and efficient work environment, aiming to achieve a balance between work and life for its members. It provides support for employees to remain committed to their jobs through the operation of an in-house welfare fund, housing funds, living stability funds, and support for the education expenses of employees’ children. Additionally, it ensures coverage for aspects not covered by workers’ compensation insurance through group insurance and supports club activities such as soccer and mountaineering to promote camaraderie and leisure activities among employees. Furthermore, it allows members with responsibilities related to childbirth and childcare to freely utilize systems such as vacation, leave of absence, and shortened work hours. It has also established a flexible work culture by introducing flexible working hours such as staggered commuting and remote work systems.
|
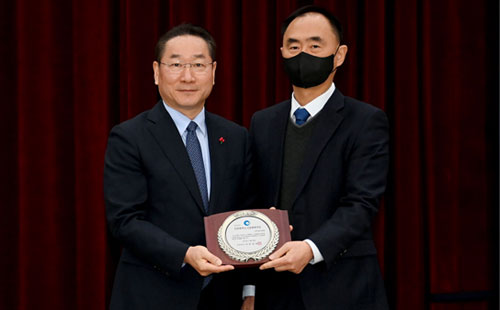 |
▪︎ Winner of the 33rd Incheon Metropolitan City Industrial Peace Award
KISCO was awarded the Incheon Metropolitan City Industrial Peace Award on December 26, 2023, for its contributions to promoting labor-management harmony and industrial peace in the local community.
|
▪︎ Cooperative Labor-Management Culture: Kyung-In Family Council, Production Division Proposal Program

To promote mutual understanding and cooperation between labor and management, KISCO operates the “KISCO Family Council” at each site at least once per quarter, aiming to enhance company development and employee welfare.
KISCO also operates an anonymous suggestion box at each workplace and continues the “Production Division Proposal System,” launched in 2020, which allows employees to freely submit and participate in improvement ideas. As of December 31, 2024, a total of 1,208 proposals have been received in areas such as quality, cost, productivity, equipment, occupational health and safety, revenue growth, work process improvement, and employee concerns.
Selected proposals are promptly implemented and their outcomes monitored, while outstanding ideas are recognized and rewarded annually to encourage active participation from employees.
|
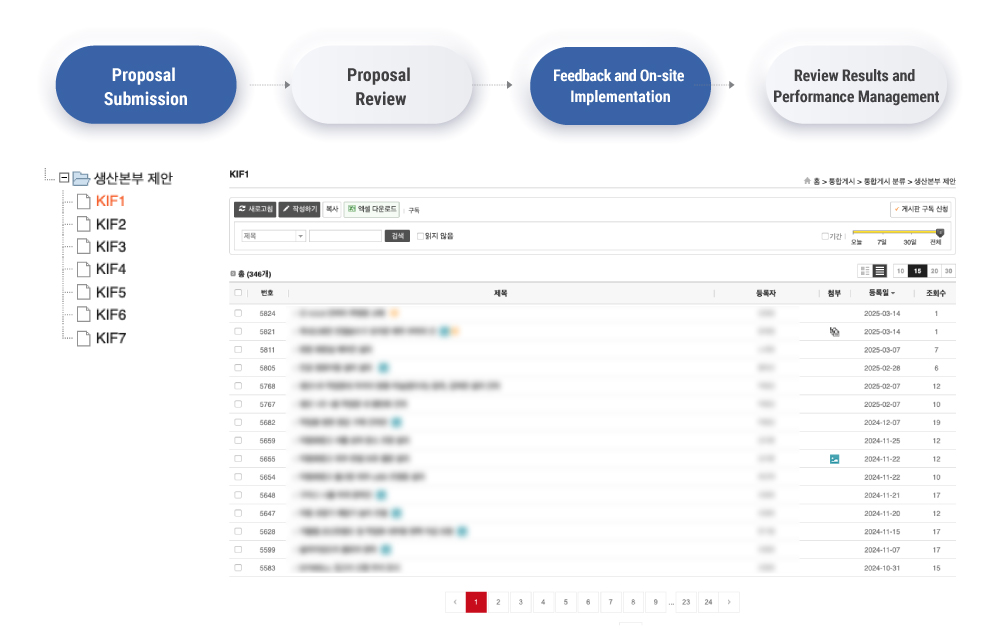
▪︎ KISCO Community Engagement Policy

KISCO establishes and implements voluntary environmental cleanup and ecosystem restoration plans in the communities where its sites are located, with the aim of fulfilling its corporate social responsibility by contributing to the creation of a pleasant living environment and improving nearby ecosystems. In addition, the company continues to engage in charitable activities to support and share with its neighbors.
|
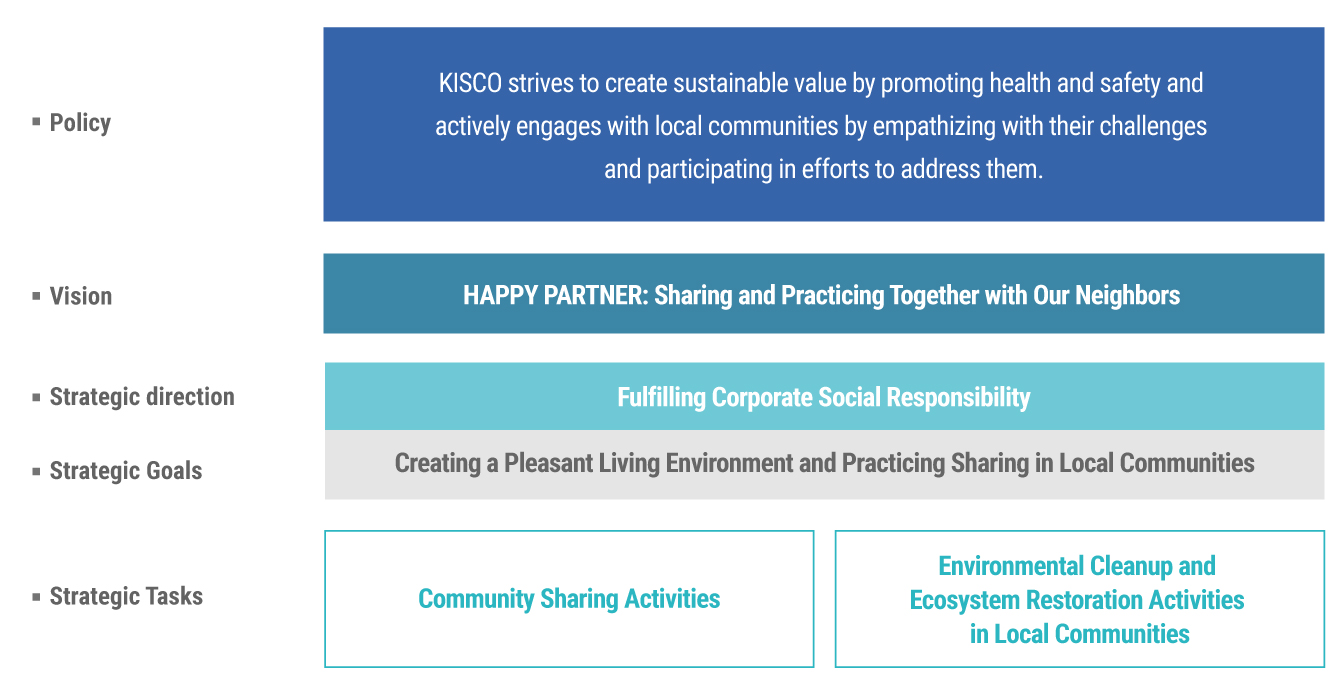
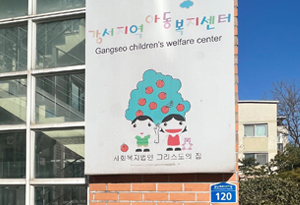 |
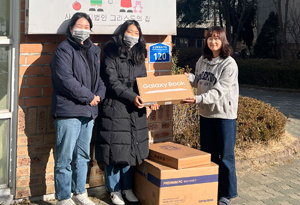 |
Employees of KISCO Central Research Institute
December 19, 2024
KISCO donated approximately 2 million KRW worth of supplies to the Zion Children’s Home in Banghwa-dong, Gangseo-gu, Seoul continuing the support for a second consecutive year.
|
▪︎ Community and Ecosystem Environmental Cleanup Activities |
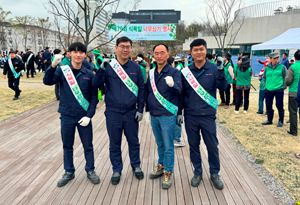 |
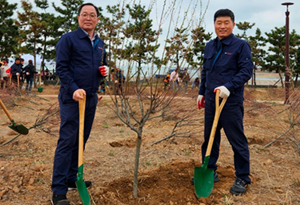 |
Participation in the 79th Arbor Day Tree Planting Event, hosted by Incheon Metropolitan City and Siheung City
April 5, 2024
Voluntary participation of KIF1 and KIF4 staff in environmental preservation and community activities through the planting of a total of 4,500 trees.
|
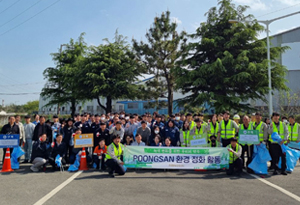 |
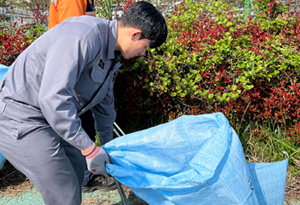 |
Participation in spring roadside cleanup in the Onsan National Industrial Complex [JMC]
April 17, 2024
Collection of approximately 3 tons of roadside waste and illegal posters within the Onsan Industrial Complex to help create a cleaner environment.
|
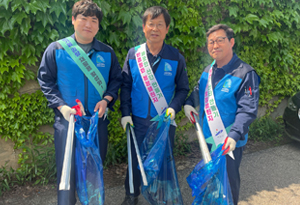 |
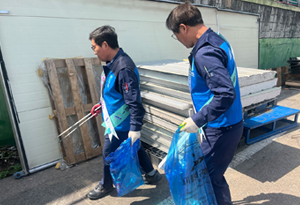 |
Participation in the Clean Ansan Industrial Complex Campaign
May 10, 2024
Voluntary participation of KIF3 staff in environmental preservation and local community activities through a regional environmental program held at Byeolmang Park, Ansan, Gyeonggi-do.
|
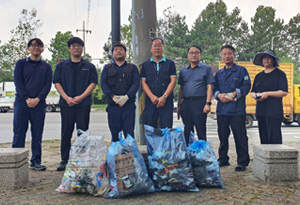 |
|
Participation in the Beautiful Industrial Complex Maintenance Campaign in Siheung
September 27, 2024
Voluntary participation of KIF4 staff in CSR activities and environmental improvement through cleanup efforts in streams, roadsides, and parks at Hope Park, Okguchun, Siheung, Gyeonggi-do.
|
▪︎ Community Service Activities in India |
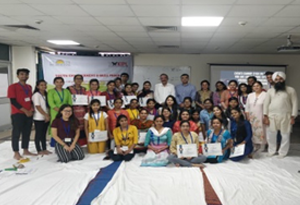 |
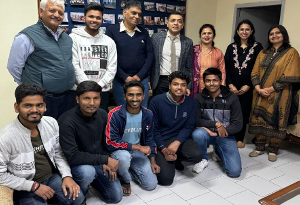 |
Scholarship funds provided to 35 students
from local universities and educational institutions
Punjab Engineering College, Chandigarh
Dr.B.R. Ambedkar National Institute of Technology
|
▪︎
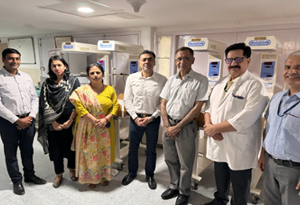 |
 |
Donation of equipment including neonatal
warming systems and TVs to local hospitals
|
▪︎ Cooperative Efforts with Partner Companies

▪︎ Safety Education for Partner Companies and Regular Council Operations |
KISCO provides daily safety training and frequent risk inspections under the supervision of safety managers to ensure a safe working environment for partner company workers. Periodic consultative bodies are also operated for each partner company to ensure smooth communication on grievances and suggestions.
|
▪︎ Supply Chain Sustainability Management Policy

KISCO aims to establish a sustainable supply chain that emphasizes human rights and environmental considerations in cooperation with its partner companies. The company has established a Supplier Code of Conduct and a Supply Chain Risk Management Process to manage the sustainability and risks of its supply chain.
It continuously enhances the transparency and management of both financial and non-financial risk factors, including human rights and environmental risks, through regular annual assessments.
|
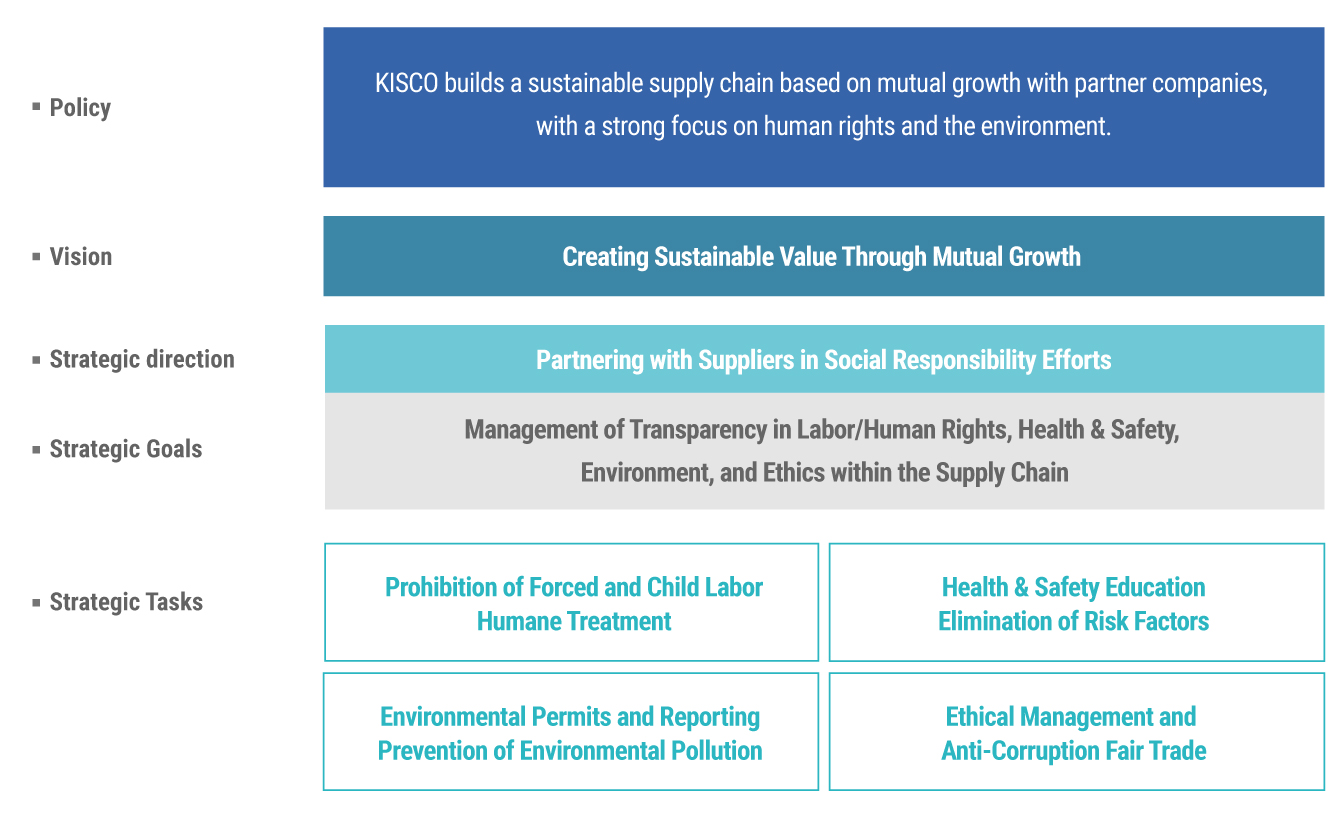
▪︎ Supplier Code of Conduct |
KISCO’s Supplier Code of Conduct was established to ensure mutual respect and co-prosperity between KISCO and its partners. It emphasizes the importance of human rights, environmental responsibility, and sustainable value creation. All partner companies are expected to comply with this code. |
▸ Download Supplier Code of Conduct |
▪︎ Supply Chain Risk Management Process |
KISCO regularly assesses and manages partner risk factors using multi-assessment methods to ensure transparency. The company is continuously enhancing its processes to build a more responsible supply chain. Annually, it evaluates at least once approximately 70% of its total annual procurement value through partner company assessments. |
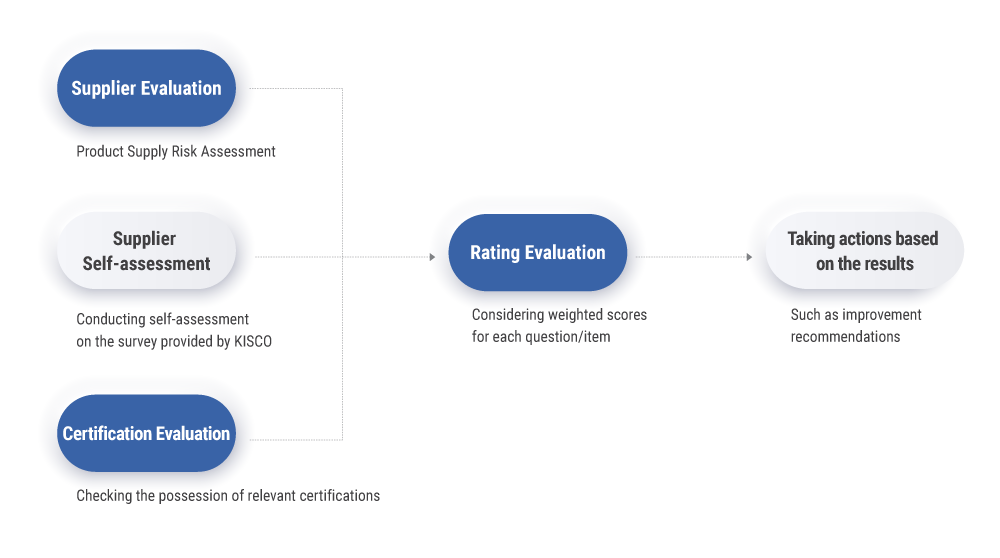
▪︎ KISCO Environment, Health and Safety Management
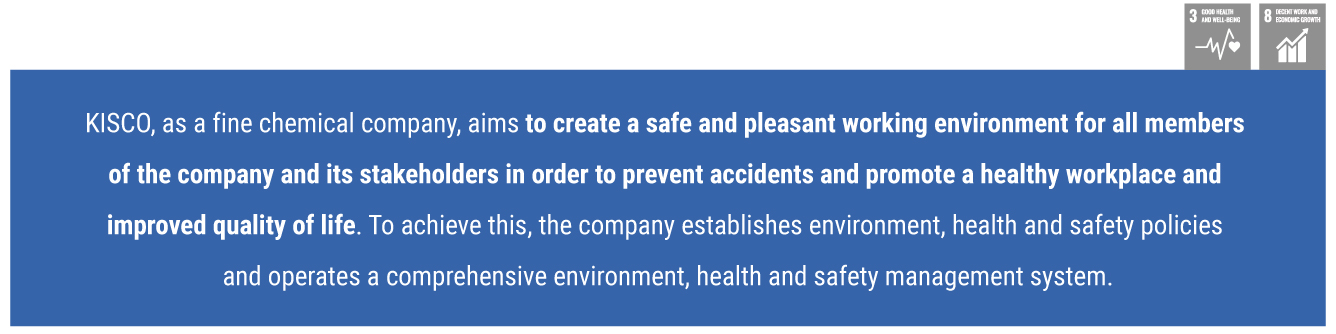
KISCO maintains an Occupational Health and Safety (OHS) policy and system to create a safe and pleasant workplace environment for all employees, partner companies, and customers. An EHS (Environment, Health, and Safety) system is implemented at all sites and operates in accordance with the international standard ISO 45001. The company conducts regular training and exercises related to occupational health, safety, and environment and operates integrated grievance handling procedures and a Production Division Proposal Program to address issues and suggestions related to EHS. |
▪︎ Environment, Health and Safety Policy
We place employee safety and health as our top priority. We identify and prevent major risk factors and environmental impacts in all product manufacturing and service activities. Through continuous investment and process improvement, we aim to maintain safe and healthy working conditions and environments — and we are committed to continuous improvement of these standards.
|
▪︎ Environment, Health and Safety Code of Conduct
▪︎ |
Establish detailed Environment, Health and Safety goals. Review and evaluate them regularly, and disclose them to all members and stakeholders |
▪︎ |
Build objectives and detailed plans through regular evaluation and inspection of systems and processes |
▪︎ |
All staff must be fully aware of company regulations and conduct themselves accordingly |
▪︎ |
Operate manufacturing processes to meet all health, safety and environmental requirements through consultation of and engagement with staff |
▪︎ Environment, Health and Safety Goals
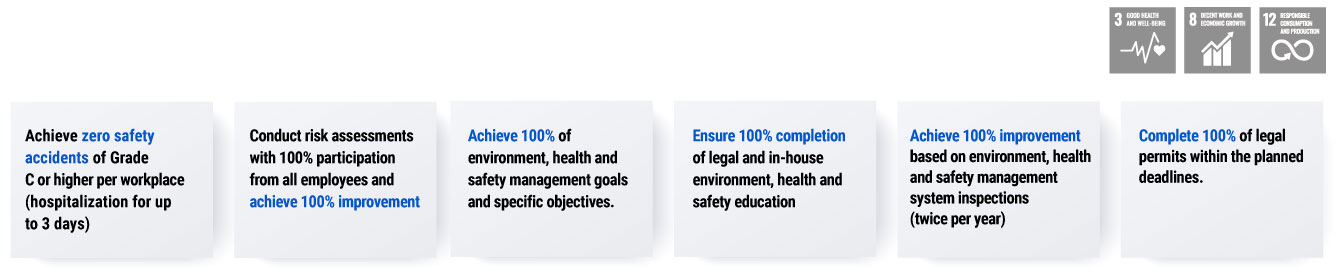
▪︎ EHS Management Organizational Chart
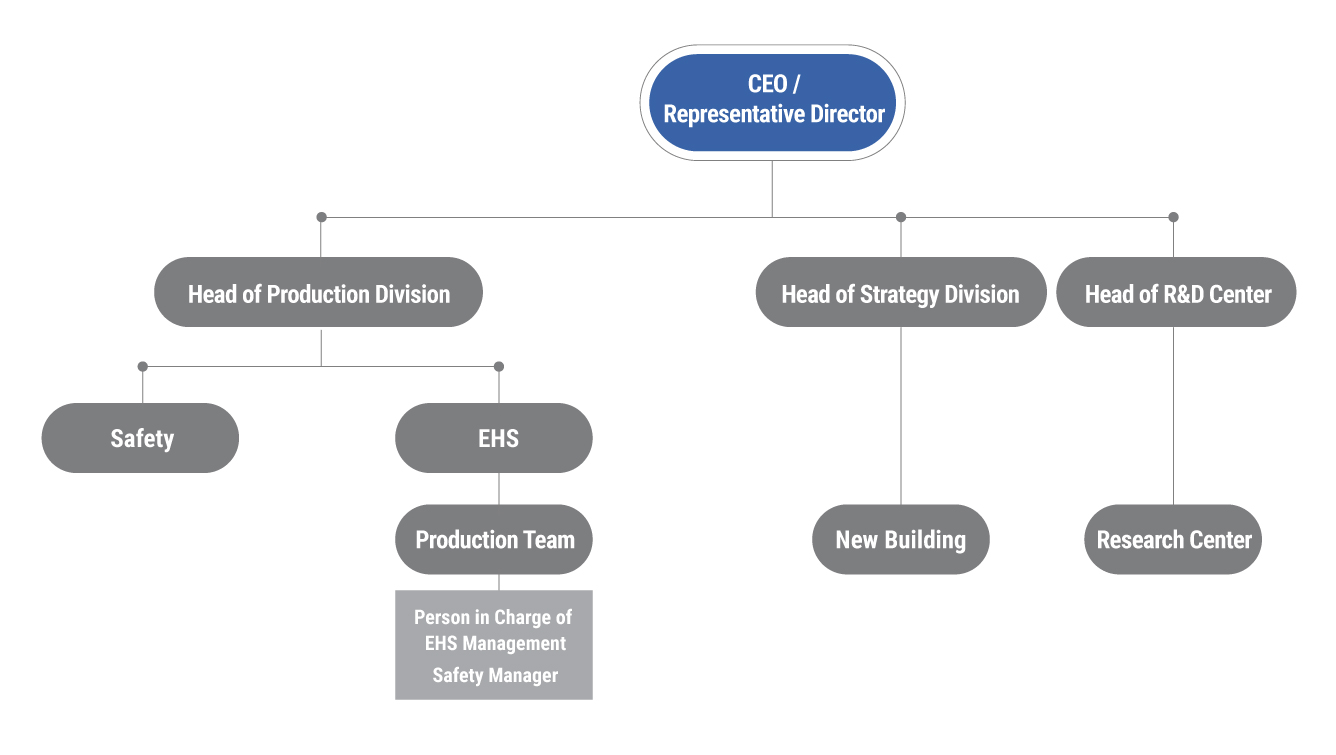 |
▪︎ EHS System

KISCO has established an Environment, Health and Safety (EHS) system and set up a dedicated organization to build a structured safety management system, prevent accidents and ensure compliance with regulations. |
▪︎ Establishment of Safety Management System (Prevention of Safety Accidents)
▪︎– Standardization of processes by task and establishment of R&R (group integrated management)
▪︎– Real-time tracking and sharing of business progress
▪︎– Integrated management of EHS systems including planning and results history
▪︎
▪︎ Establish a Regulatory Immediate Response Foundation
▪︎– Timely licensing based on new/modified items
▪︎– Integrated schedule management to prevent delays/misses in rental business
▪︎– Establish a regulatory response system by strengthening EHS-related laws
|
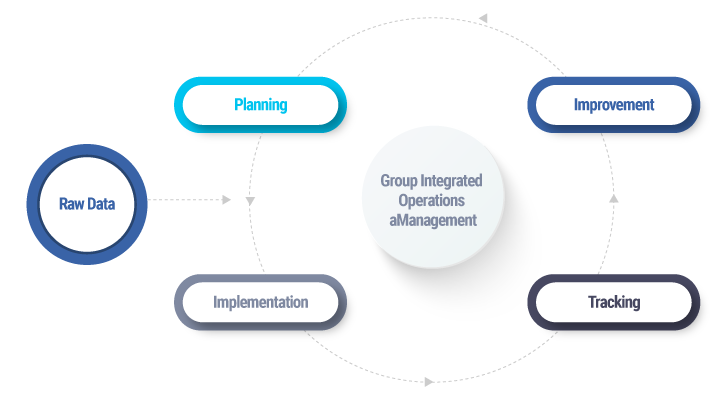 |
▪︎ EHS System Key Management Points
|
Preventative
Inspections
Safe Work
Permits
|
Change Factor
Management
Contractor Safety
Management
|
Pre-Operation
Safety Checks
License
Management
|
Regular Facility
Inspections
Qualified Senior
Management
|
Near-Miss Accident
Management
Self-Test
PSM
|
▪︎ KISCO Occupational Health and Safety Committee

To prevent injuries and accidents, health and safety plan updates and improvement measures are agreed once a quarter through these Industrial Health and Safety Committees. Emergency action plans are regularly updated through this consultation process. |
▪︎ Health and Safety Committees Operation Goals
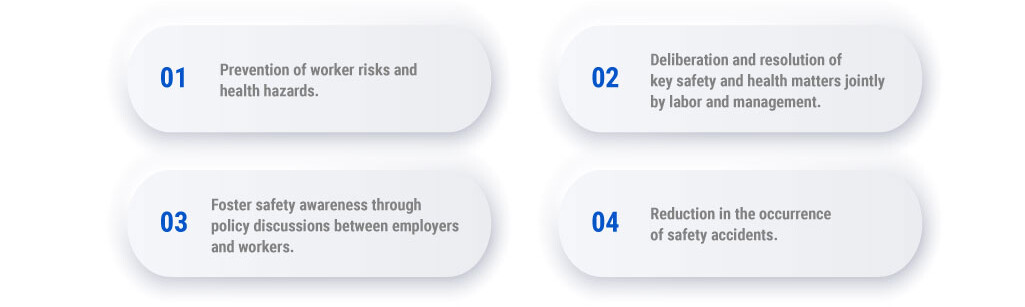 |
▪︎ Committee Structure and Operation |
– Committee Chair: Jointly chaired by management and employee representatives
– Committee Members: 5 management representatives + 5 employee representatives from each business site (equal number)
– Regular quarterly meetings and additional meetings held when deemed necessary by the chair |
▪︎ Occupational Health and Safety Risk Assessment
KISCO has implemented and operates ISO 45001 (Occupational Health and Safety Management System). Based on this, regular and ad-hoc risk assessments are conducted at least twice a year under the supervision of the EHS organization across all KISCO domestic sites, including non-certified ones.
|
▪︎Employee Health Management Status

KISCO conducts various environmental, health and safety education and training programs to enhance the safety competency of its employees. It also conducts emergency response training for incidents such as fire, explosion, and chemical leaks to prepare for safety accidents.
|
▪︎
Types |
Cycle |
Training Hours |
For Whom |
Training for new hires |
Upon new hiring (as needed) |
8 hours |
New hires |
Special health and safety training |
Occasional |
16 hours |
First person assigned to work |
Supervisor training |
24.2.1~12.10 |
16 hours |
Senior manager |
Regular health and safety education |
24.1.2~12.31 |
6 hours/quarter |
All employees |
Health and safety manager training |
24.1.2~12.31 |
6 hours/2-year |
Senior manager |
Process safety training |
24.1.2~12.31 |
Over 4 hours |
Target process workers |
Risk assessment training |
24.1.2~12.31 |
2 hours |
All production sites staff |
Material Safety Data Sheet (MSDS) |
24.1.2~12.31 |
Over 1 hours |
All production sites staff |
Emergency response training |
24.4.1~12.24 |
2 time |
All employees |
Hazardous chemicals manager training |
24.1.2~12.31 |
16 hours/2-years |
Hazardous chemicals manager |
Hazardous chemicals handler training |
24.1.2~12.31 |
16 hours/2-years |
Hazardous chemicals handler |
Hazardous chemicals workers training |
24.1.2~12.31 |
2 hours |
Handling of hazardous chemicals |
Training for hazardous materials safety managers |
24.1.2~12.31 |
Over 4 hours |
hazardous materials safety managers |
Training for inspectors |
24.1.2~12.31 |
2 hours |
Plant Facility Inspectors |
* If training hours vary by site and topic, the minimum conducted hours are recorded.
▪︎
▪︎ Safety Training for Partner Companies (Conducted Daily) |
KISCO conducts daily safety training for partner company members before work, and regularly conducts inspections of potential hazards under the supervision of safety managers to ensure the safety of partner company employees. |
▪︎ Emergency Response Training |
Number |
Scenario title |
Quantitative Evaluation |
Implementation Status of Emergency Response Drills |
2022 |
2023 |
2024 |
1 |
Chemical leak accident |
◎ |
● |
● |
● |
2 |
Fire explosion accident |
◎ |
● |
● |
● |
3 |
Emergency Response Drill |
✕ |
● |
● |
● |
▪︎
▪︎ Major Safety and Health Activities

▪︎ Zero Safety Accidents |
– Daily safety patrols at all plants, with follow-up actions and improvement measures based on inspection results
– Biannual thematic safety inspections at each plant, with plant-specific corrective and improvement actions based on findings |
▪︎ Working Environment Management |
– Workplace environment monitoring and risk assessments
– Internal inspections of hazardous chemical handling facilities
– Functional inspections of fire protection systems
– Safety inspections of fire safety equipment |
▪︎ Process Safety Management (PSM) consulting |
– Activities to improve and strengthen a safety culture within the organization |